Disposable paper cups are everywhere in our lives. We use paper cups in our daily life. It improves our life quality and makes our life more convenient. But, this “Disposable” is really safe and sanitary? How to make a paper cup? Here, we will guide you.
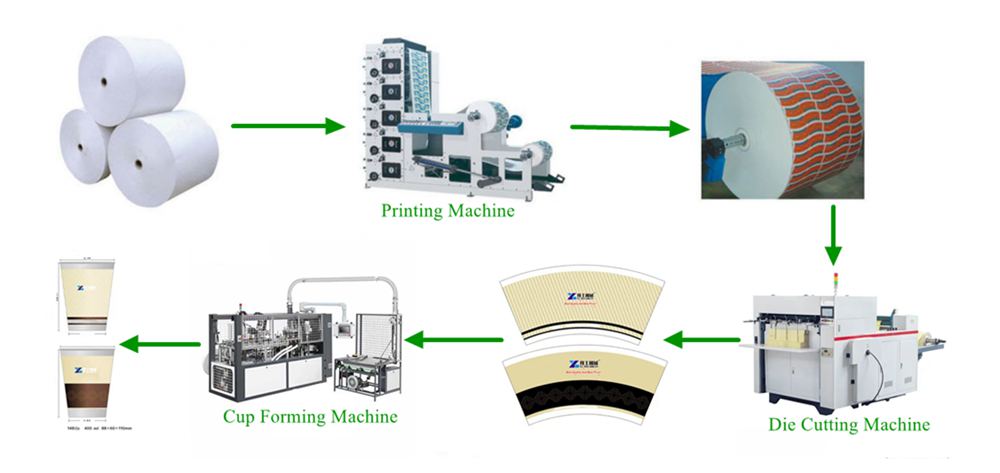
How to make paper cup with a cup forming machine?
Of course, we can make paper cups manually. But in the industry period, that is not very usual. In this article, we will show you the production process of paper cups with a tea cup forming machine.
Raw material – Paper roll
First of all, the paper used to make the paper container must be food-grade paper. Then, carry out the process of laminating. Coating the material that can resist oil and water before the subsequent forming steps.
Remark: The coating is a very thin layer of plastic material attached to the paper, which makes the paper cup resistant to oil and water, and can hold beverages and soups for a long time. The selection of this coating material is also related to the characteristics of the subsequent paper cups. This is the step to make the paper cup sturdy and beautiful.
Printing
After the lamination treatment, we will print the desired pattern and color on the paper roll. Printing methods can be divided into 3 methods: gravure, convex plate, and flat plate. The cost of gravure is too high, and it is now rarely used; letterpress printing is continuously printed on paper rolls, and the required printing volume is large. Lithographic printing, in which paper is cut into pieces and then printed, is suitable for making small quantities of products. After the ink is applied, another layer of water gloss treatment will be printed as protection. According to your needs, you can print your company logo and contact information on the cup.
New technology for printing: Digital printing solutions for paper cups
Cutting
Die cutting machine will cut the paper roll according to the paper cup size.
The printed paper enters the knife mold and produces a fan-shaped piece of paper, which is the unfolded shape of the wall of the paper cup. Then the fan-shaped paper is collected and sent to the forming machine.
Forming
For making a paper cup, we need to make the cup’s body and the cup’s bottom. The cup body uses the paper fan as raw material. The bottom of the disposable paper cup is to cut out paper rolls of different specifications.
The paper fan is then rolled out of the cup mold into the shape of a paper cup. At the same time, the mold provides heat at the seam of the paper, so that the PE is thermally destroyed and adhered to each other. And the bottom of the paper cup is then glued. Immediately after the mold pushes the mouth of the cup, the paper at the mouth of the cup is rolled down and fixed by heat to form the rim of the paper cup. These forming steps can be completed in one second.
Then send completed paper cups to the inspection machine to confirm whether the shape is complete without damage and whether the inner surface is clean and free of stains.
Because the cost of printing and die-cutting does not account for a small proportion of the cost in the production of paper cups and paper bowls, the cost is mainly determined by the size of the paper cup and the weight of the paper. If you want to start a paper cup manufacturing business, you can contact us to get a free quote for the paper cup making machine.
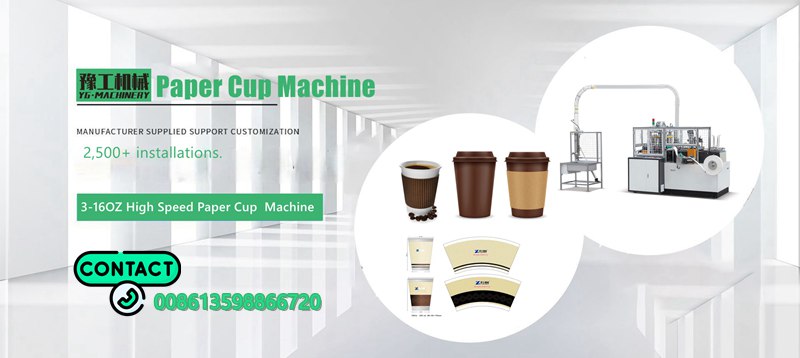
Paper cups for hot drinks need coating but can not be waxed. Because the heat can cause the wax to melt and be harmful to the body.
Differences between the production process of the cold drink paper cup and hot drink paper cup
The production process of the cold drink paper cup machine is direct printing, die-cutting, forming and double-sided lamination from the paper cup base paper. The production process of the hot drink paper cup machine is that the paper cup base paper is coated into paper cup paper, printing, die-cutting, and forming.
The paper cup machine is composed of base paper and plastic resin particles extruded and compounded. Plastic resin generally uses polyethylene resin (PE). The cup base paper is coated with single-sided PE film or double-sided PE film to become single-PE or double-PE paper cup paper.
Production operation process of Paper Cup Machine
- Material preparation. PE coated paper inspection: The purchase of coated paper meets the requirements of GB9687-1988 for polyethylene molded products for food packaging; the color is normal, and smooth, with no obvious wrinkles, no smell, and no dirt.
Design printing patterns according to customer requirements, and send the produced film to the printing room for plate making.
The printed sheet after printing. Send to indentation workshop for cutting. And separate the corner blanks. Arrange the separated fan-shaped cup blanks according to the specified quantity. - Turn on the main power supply, heating power supply, and host power supply of the cup-making equipment, heat for 30 minutes, and then turn on the dehumidifier and the host motor;
- Place the cut cup body paper neatly in the fixture. According to the temperature and humidity of the workshop, water the paper and wait; the installation and debugging of the bottom paper: It is required to be moderately tight and in place on the left and right.
- Turn on the air compressor and supply air to the equipment. Set the bottom bonding temperature to 230℃~300℃, and the speed to be 40-50 pieces/min; the ultrasonic wave time of the cup wall is 2~3 seconds.
- Turn on the main unit switch for a few seconds and wait for the supply of the backing paper to be normal; then put down the cup wallpaper fixture, and the suction cup starts to transport the cup wallpaper into ultrasonic welding.
- Observe whether the mechanical movement of the bottom paper feeding, knurling, cup rolling, finished product unloading, and other processes are smooth;
- Check the adhesion of the bottom of the cup to see if there are any undesirable phenomena such as water leakage and water seepage;
- Collect and sort out the finished product after unloading;
- Check whether the finished product is defective and qualified;
- Disinfection of qualified products;
- Pack the finished product and put it into storage.
In conclusion
In recent years, with the improvement in people’s quality of life, the number of paper cups is increasing. And the demand for paper cup production equipment has also increased significantly. If you have an interest in paper cup forming machine, please leave your messages. Or contact us to get a free quote.