Everyone must be familiar with the paper. This is the product that is second only to water in our daily use. But have you ever thought about how is made paper? Maybe many readers know that it is made of trees. Do you know the specific production process? Today, I will give you a detailed explanation of a series of paper production processes. So read on.
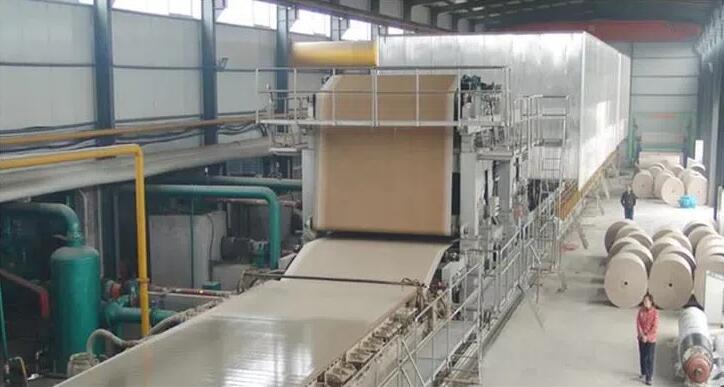
Types of the paper and paperboard
What are the types of paper? There are 11 categories of paper and 6 categories of cardboard.
11 types of paper: printing paper, writing paper, drawing and drawing paper, electrical insulating paper, cigarette paper, suction paper, instrument paper, photosensitive paper, transfer paper (base paper), industrial technical paper, and packaging paper.
6 categories of cardboard: binding cardboard, box-making cardboard, insulating cardboard, industrial technical cardboard, construction cardboard, and shoe-making cardboard.
Read more
High Speed Automatic Kraft Paper Bag Making Machine for Sale
Raw Materials to make Paper
The production of paper starts from the raw materials which can be one of these things: Cellulosic pulp from trees, waste that turns into sawdust, or the recycled paper itself, although cloth, flax, lint, and sugarcane residues.
Good quality raw materials are the basis of the paper of high quality.
Note
If your budget is limit, you can consider using waste paper or wood pulp board as the raw materials to manufacturing the paper; If you have a strong investment, then you can choose the raw materials like wood, straw, reed, wheat straw… all of which can be used to make paper. In general, this type of Paper machines has a relatively large production capacity.
How is paper made from trees?
Wood is a common raw material to make paper. Here we will introduce step by step how to make paper from trees or woods.
Fell trees
Premium paper is made from wood grown in sustainably managed forests and plantations. The wood used for production comes either from deciduous trees such as birch, poplar, birch, and eucalyptus or from conifers such as spruce-fir and pine.
Removes the bark and shredding
When the logs arrive at the woodyard, you can feed them into a rotating drum that removes the bark and then shreds it with a wood shredder. By the way, the scrap from industrial sawmills is the largest source of wood chips for papermaking.
Make the pulp
Then you need to transport the wood chips to the pulp mill through conveyor belts. When they enter the pulp mill, the digester starts working. When cooked in an acidic solution to dissolve the lignin and separate plant fibers. Remark: Since the lignin has dissolved, we call the pulp obtained from this process free of wood.
Remove fibers
The fibers are washed to remove the acid solution and the pulp is now soft and fibrous. Before making white paper, the pulp is bleached and then filtered to remove any residual lignin that would cause it to turn yellow over time. To protect the environment, this bleaching can be chlorine-free bleaching using oxygen and peroxide. The yellow-brown wood chips that enter the pulp mill are now turned into white pulp, which is the main raw material for making paper.
Transport paper mills
This treated pulp can be dried, baled, and transported to other paper mills that may not have their own pulp mills or that require specific types of pulp to impart their special properties. Whether you want to produce on-site or purchase in the market, you need always mix the pulp with water.
Make paper rolls
In this step, you need to refine the pulp through a series of rotating and stationary blades. Fibrillated fibers bond more tightly to adjacent fibers, resulting in a stronger paper.
Press and DRY
Now comes the press section. A hydraulically driven metal pad will press the wet paper and squeeze water out of the paper. A drying cylinder dries it, making it a self-supporting strength.
Drying processes and technologies play a vital role in improving paper quality.
After pressing and drying, the paper will pass through the paper machine at speeds of up to 1400 meters per minute. Spray the color of the paint onto the rollers, and then transfer it to the paper web.
Cutting
Finally, the rotary cutting machine will cut and roll the paper web into a large roll-up of 80 km long.
Voila. And then, you can use a packaging machine to pack the paper and sell it to other paper productions factory, such as tissue paper manufacturing factories.
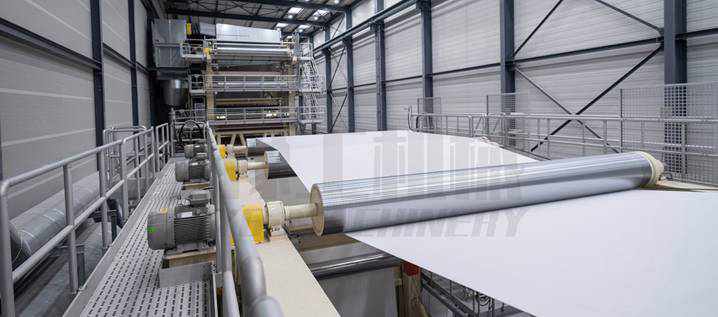
Read also
How is toilet paper made? | History, manufacturing, top brands
Conclusion
All of us use paper every day or almost every day. Of course, we can make paper out of trees. But to protect the environment, it is better to use the wasted scrap to produce eco-friendly recycled paper. One ton of waste paper can produce 850 kilograms of recycled paper with good quality, save 3 cubic meters of wood (equivalent to 26 trees of 3 to 4 years old), save 300 kilograms of chemical raw materials, save 1.2 tons of coal, and save 600 degrees of electricity; and reduce a lot of waste. Also, your investment in the paper business will not be that large.